真空動密封
Vacuum dynamic seal
在進行噴淋清洗或超聲波浸漬清洗時,工件籃在電機帶動下旋轉(zhuǎn),此時腔體內(nèi)真空度為(5~8)kPa,為防止外部空氣進入真空腔,需要在電機軸與腔體連接處進行動密封,一般是采用機械密封裝置,并在機械密封與旋轉(zhuǎn)軸之間、機械密封本體內(nèi)均注入潤滑油達到動密封效果。
When performing spray cleaning or ultrasonic immersion cleaning, the workpiece basket rotates under the drive of the motor. At this time, the vacuum inside the cavity is (5-8) kPa. To prevent external air from entering the vacuum cavity, it is necessary to install a movable seal at the connection between the motor shaft and the cavity. Generally, a mechanical seal is used, and lubricating oil is injected between the mechanical seal and the rotating shaft, as well as into the mechanical seal body, to achieve the effect of dynamic sealing.
與常規(guī)動密封不一樣,碳氫設(shè)備動密封面臨一個難題:隔離對象是空氣及碳氫溶劑。碳氫溶劑本身是可以溶解潤滑油的,而且碳氫溶劑表面張力小,滲透力強,特別在超聲波作用下,對油脂的溶解效果更加明顯,長時間的運轉(zhuǎn),是否會將潤滑油脂溶解掉而造成泄漏及旋轉(zhuǎn)干磨。因此,如何做好碳氫溶劑的真空動密封是碳氫設(shè)備研發(fā)的一個難點。
Unlike conventional dynamic seals, hydrocarbon equipment dynamic seals face a challenge: the isolation objects are air and hydrocarbon solvents. Hydrocarbon solvents themselves can dissolve lubricating oil, and their surface tension is small and their permeability is strong. Especially under the action of ultrasound, the dissolution effect of oil and grease is more obvious. Will long-term operation dissolve the lubricating oil and cause leakage and rotary dry grinding. Therefore, how to do a good job in vacuum dynamic sealing of hydrocarbon solvents is a difficulty in the development of hydrocarbon equipment.
溶劑回收
Solvent recovery
在進行溶劑真空蒸餾回收時,蒸餾釜加熱產(chǎn)生的蒸汽中包括空氣、溶劑蒸汽、水蒸氣,溶劑中含水會造成清洗零件的氧化,因此需要大限度的降低水含量。碳氫溶劑與水的分離一般有兩種方式(假定在真空壓力p、溫度t1處進行蒸餾)。1)保持壓力,降低冷凝區(qū)溫度t2,碳氫蒸汽先開始液化,保持t2一段時間,直到碳氫蒸汽完全液化,剩余氣體為水氣及空氣。2)保持溫度不變,降低真空度,增加冷凝區(qū)壓力,水蒸氣先開始液化,保持該真空度一定時間直到水氣完全液化,剩余氣體為碳氫蒸汽及空氣。
When conducting solvent vacuum distillation recovery, the steam generated by heating the distillation kettle includes air, solvent steam, and water vapor. Water in the solvent can cause oxidation of the cleaned parts, so it is necessary to minimize the water content. There are generally two ways to separate hydrocarbon solvents from water (assuming distillation at vacuum pressure p and temperature t1). 1) Maintain pressure and lower the temperature of the condensation zone to t2. The hydrocarbon vapor begins to liquefy and remains at t2 for a period of time until the hydrocarbon vapor is completely liquefied, with the remaining gas being water and air. 2) Maintain the temperature unchanged, reduce the vacuum degree, increase the pressure in the condensation zone, and water vapor begins to liquefy. Maintain this vacuum degree for a certain period of time until the water vapor completely liquefies, and the remaining gas is hydrocarbon vapor and air.
性設(shè)計
Security design
1)防止泄漏。為防止泄漏(或在泄漏時盡量減少泄漏量),需要從多方進行考慮。一是在各腔體、各管系的適當位置均設(shè)置壓力檢測,所有的檢測值均引入PLC,并與PLC內(nèi)事先存儲的設(shè)定值進行比較,若與設(shè)定值差異很大,則關(guān)斷工作電源并報警;二是管系上各主要器件之間均設(shè)置氣控閥,當其中一段發(fā)生泄漏時,可將該段兩端的氣控閥關(guān)閉,將泄漏量降到低,三是氣控閥及控制氣閥的電磁閥均采常閉閥,確保斷電即斷氣,確保管系能分段隔離。
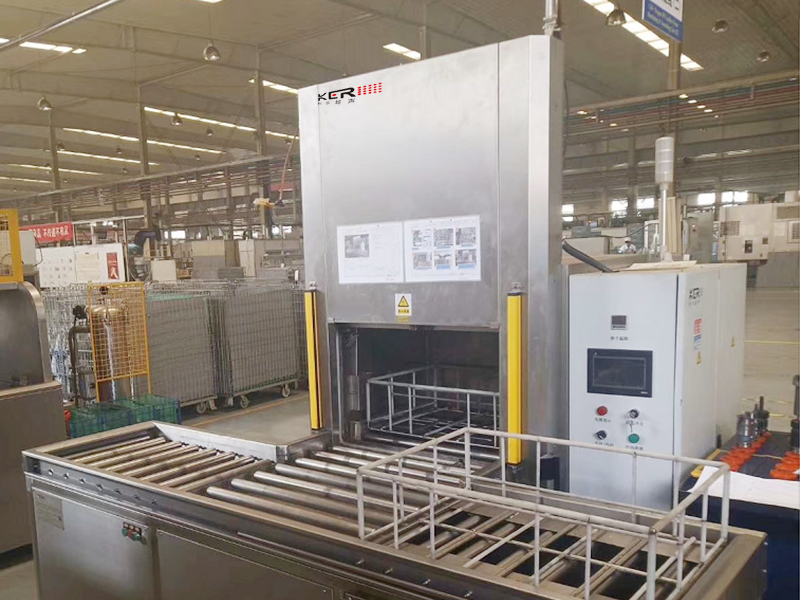
1) Prevent leakage. To prevent leakage (or minimize the amount of leakage when leaking), it is necessary to consider multiple factors. Firstly, pressure detection is set at appropriate positions in each cavity and pipeline system, and all detection values are introduced into the PLC and compared with the preset values stored in the PLC. If there is a significant difference from the set value, the working power is turned off and an alarm is given; Secondly, air control valves are installed between the main components on the pipeline system. When a leakage occurs in one section, the air control valves at both ends of the section can be closed to minimize the leakage. Thirdly, both the air control valve and the solenoid valve controlling the air valve adopt normally closed valves to ensure that the power is cut off immediately and the pipeline system can be isolated in sections.
2)蒸汽濃度監(jiān)測。在設(shè)備內(nèi)部高位、中位、低位設(shè)置多處碳氫蒸汽濃度檢測,并設(shè)置合理的爆炸下限,達到下限時,設(shè)備斷開工作電源,并啟動報警。
2) Steam concentration monitoring. Multiple hydrocarbon vapor concentration detections are set at the high, middle, and low positions inside the equipment, and reasonable explosion safety limits are set. When the lower limit is reached, the equipment disconnects the working power supply and initiates an alarm.
3)杜絕明火。一是在設(shè)備內(nèi)部的電機,如旋轉(zhuǎn)電機、真空泵用電機等均采用防爆電機;管系所用控制閥均為氣動閥,控制氣動閥的電磁閥均安裝在單獨的電控箱內(nèi);電控箱與設(shè)備完全隔離,對電控箱與設(shè)備之間的穿線孔全部進行密封;電機、腔體、管系及機架等均良好接地,避免靜電產(chǎn)生。
3) Eliminate open flames. One is that the motors inside the equipment, such as rotating motors and vacuum pump motors, are all explosion-proof motors; The control valves used in the pipeline system are all pneumatic valves, and the solenoid valves that control the pneumatic valves are installed in separate electric control boxes; The electric control box is completely isolated from the equipment, and all wiring holes between the electric control box and the equipment are sealed; The motor, cavity, piping, and frame are well grounded to avoid static electricity generation.
4)自動滅火。在設(shè)備內(nèi)部高位、中位、低位設(shè)置多處煙氣檢測點,并設(shè)置自動二氧化碳滅火器。在檢測到燃燒時,切斷工作電源,啟動二氧化碳滅火并報警。當滅火完全后,啟動強排裝置,將碳氫蒸汽及二氧化碳排出設(shè)備。
4) Automatic fire extinguishing. Multiple smoke detection points are set up at the high, middle, and low positions inside the equipment, and automatic carbon dioxide fire extinguishers are installed. When combustion is detected, cut off the working power supply, activate carbon dioxide fire extinguishing and alarm. After the fire is completely extinguished, start the forced exhaust device to discharge the hydrocarbon vapor and carbon dioxide from the equipment.