表面處理是輕工行業(yè)的組成部分,包含機(jī)械零件電鍍,金屬和非金屬機(jī)箱柜涂覆、光學(xué)玻璃或鏡片鍍膜等,而電鍍工藝產(chǎn)品清洗,對(duì)工件表面清潔度要求較高,超聲波清洗技術(shù)已成為了新的電鍍處理清洗工藝需求,是達(dá)到工藝要求的理想技術(shù)。
Surface treatment is an integral part of the light industry, including electroplating of mechanical parts, coating of metal and non-metal chassis and cabinets, coating of optical glass or lens, etc. the product cleaning of electroplating process has high requirements for the surface cleanliness of workpieces. Ultrasonic cleaning technology has become a new electroplating cleaning process demand and an ideal technology to meet the process requirements.
超聲波清洗電鍍前處理的應(yīng)用,主要利用超聲波在液體中產(chǎn)生的空化效應(yīng),可以清洗掉工件表面沾附的油污,配合適當(dāng)?shù)那逑磩梢匝杆俚貙?duì)工件表面實(shí)現(xiàn)高清潔度的處理。另外,利用超聲波清洗技術(shù),還可以在很大的范圍內(nèi)替代強(qiáng)酸、強(qiáng)堿的作用,大大減少對(duì)環(huán)境的污染,并改善工人的勞動(dòng)環(huán)境,降低勞動(dòng)強(qiáng)度,對(duì)保護(hù)生態(tài)環(huán)境,作出貢獻(xiàn)。
The application of ultrasonic cleaning electroplating pretreatment mainly uses the cavitation effect produced by ultrasonic in liquid to clean the oil stain on the workpiece surface. With appropriate cleaning agent, it can quickly realize high-definition cleanliness treatment on the workpiece surface. In addition, the use of ultrasonic cleaning technology can also replace the role of strong acid and alkali in a large range, greatly reduce the pollution to the environment, improve the working environment of workers, reduce labor intensity, and contribute to the protection of the ecological environment.
超聲波清洗工藝情況簡(jiǎn)單介紹:
Brief introduction to ultrasonic cleaning process:
1.拋光件表面拋光膏的清洗
1. Cleaning of polishing paste on the surface of polishing parts
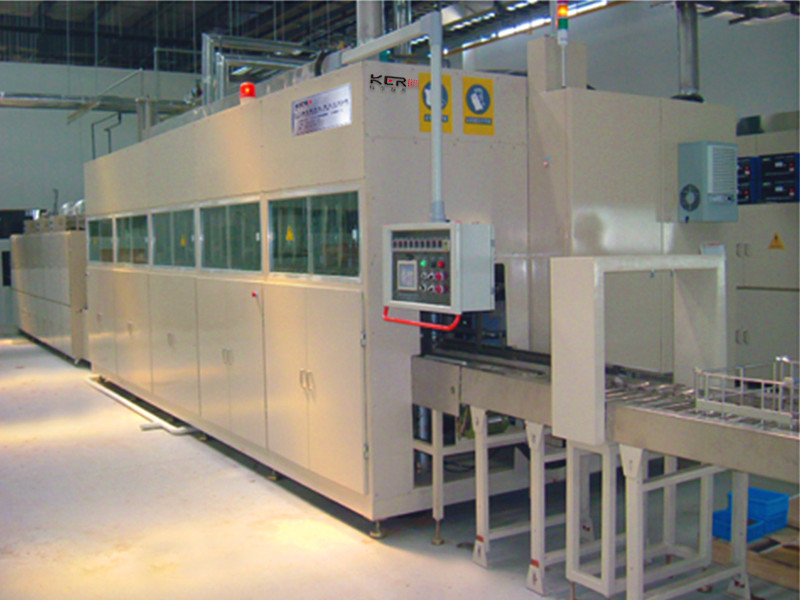
一般情況下,拋光膏常常采用石蠟調(diào)和,石蠟分子量大,熔點(diǎn)較高,常溫下呈固態(tài),是較難清洗的物質(zhì),傳統(tǒng)的辦法是采用有機(jī)溶劑清洗或高溫堿水煮洗。采用超聲波清洗則可使用水基清洗劑,在中溫條件下,幾分鐘內(nèi)將工件表面徹底清洗干凈,常用工藝流程是 :① 浸泡一②超聲波清洗一③清水(凈水)漂洗。
In general, polishing paste is often mixed with paraffin. Paraffin has large molecular weight, high melting point and is solid at room temperature. It is a difficult substance to clean. The traditional method is to clean with organic solvent or boil with high-temperature alkali water. If ultrasonic cleaning is adopted, water-based cleaning agent can be used. Under medium temperature conditions, the workpiece surface can be completely cleaned within a few minutes. The common process flow is: ① soaking - ② ultrasonic cleaning - ③ rinsing with clean water (purified water).
2.表面有油及少量銹的冷軋鋼板
2. Cold rolled steel plate with oil and a small amount of rust on the surface
冷軋鋼板表面一般有油、污或少量鐵銹,要洗干凈比較容易,但經(jīng)一般方法清洗后,工件表面仍殘留一層非常細(xì)薄的浮灰,影響后續(xù)加工質(zhì)量,有時(shí)不得不再采用強(qiáng)酸浸泡的辦法去除這層浮灰。而采用超聲波清洗并加入適當(dāng)?shù)那逑匆?,可方便快捷地?shí)現(xiàn)工件表面徹底清潔,并使工件表面具有較高的活性,有時(shí)甚可以免去電鍍前酸浸活化工序。
The surface of cold-rolled steel plate generally has oil, dirt or a small amount of rust, which is easy to clean. However, after general cleaning, there is still a very thin layer of floating ash on the workpiece surface, which affects the subsequent processing quality. Sometimes, the method of strong acid immersion has to be used to remove this layer of floating ash. Using ultrasonic cleaning and adding appropriate cleaning solution can easily and quickly realize the thorough cleaning of the workpiece surface, and make the workpiece surface have high activity. Sometimes, it can even avoid the acid leaching process before electroplating.
3.表面有氧化皮和黃銹的工件
3. Workpieces with oxide scale and yellow rust on the surface
傳統(tǒng)的辦法是采用鹽酸或硫酸浸泡清洗。如采用超聲波綜合處理技術(shù),可以快捷地在幾分鐘內(nèi)同時(shí)去除工件表面的油、銹 ,并避免了因強(qiáng)酸清洗伴隨產(chǎn)生的氫脆問題。
The traditional method is to soak and clean with hydrochloric acid or sulfuric acid. If the ultrasonic comprehensive treatment technology is adopted, the oil and rust on the workpiece surface can be removed quickly and simultaneously in a few minutes, and the problem of hydrogen embrittlement caused by strong acid cleaning can be avoided.
The above is the wonderful content brought to you by the manufacturer of ultrasonic cleaning machine. For more wonderful content, please click: http://www.zjfsmy.com We will have more wonderful content for you to check later